The Long Table
I read somewhere that there's no such thing as middle-size business, which helps explain why a strain of design like the beautiful old Hawaiian shirts couldn't persist. Those fabrics were mostly printed on long tables, a labor-intensive technique that depends on two people stepping a large screen along a piece of fabric. The tables are still used in slow-paced economic settings, but in the industrial west they've evolved into high-speed machines.
The table in the picture is the direct ancestor of the printing apparatus described later. Alternatively, an extremely useful table can be assembled from a sheet of plywood or particleboard with a two-inch steel angle running along one side.
The background in the picture is a fabric repeat I deliberately constructed to function as an overall print, or a stand-alone T-shirt design. I think there's interesting ground between the printed T-shirt and the cut-and-sewn garment that might become more accesible when digital fabric printing comes on line, although that technology is likely to remain the exclusive property of big business for awhile.
Printing T-shirts makes economic sense: build two of the tabletop printers described below and you're in business. The long tables are another matter: preferably a plant should have a hundred yards or so of these surfaces, but that quantity of fabric is still "piece goods". Nevertheless, one reason the old fabric was so beautiful is that the tables had to be long because garments need to be cut from whole cloth, which guaranteed that each color was dry before the next one went on. This made a certain precision of detail available to the designers; however they couldn't design for that level of finish unless they had access to the process, in other words be able to go to the plant and see a strikeoff.
The old Aloha shirts were an example of how good this type of fabric design can get. For lots of examples look up:
THE HAWAIIAN SHIRT,
by H.T. Steele (Abbeville Press).
I think it's a good idea to keep one's methods as independent as possible of anything but the basics, a screen and a squeegee, which is the way it's carried on as a printmaking medium in the arts where the major effort tends to be focused on image preparation, rather than equipment and technique.
Briefly, these consist of:1. A frame stretched with a fabric that will allow viscous liquids to pass where the openings are not blocked with a stencil; 2.a plastic or rubber blade is used to force liquid throughTo get started I'd recommend having on hand one or two 17 x 20in. screens with 110 mesh fabric [160 mesh for photos], plus a 12in.X70 durometer squeegee (durometer refers to hardness) . There's a list of suppliers at the bottom of this page.
I'm going to describe a few strategies for positioning a screen and pulling a good print. Bear in mind that in that solving registration and particularly color printing problems invariably leads to the accumulation of various kinds of apparatus, which while facilitating certain operations invariably limits others. The size of a silkscreen, for instance, is only limited by fabric width--it's the mechanisms used to stabilize it that limit practical working area.
Simply holding a screen down on a T-shirt with a stack of newspapers inside establishes a flat surface to print on by getting the rest of the shirt out of the way. If the print can stand a certain amount of variation it's OK to simply have your friend hold the screen while you pull the squeegee. The famous screenprinter Andy Warhol worked this way--he courted variability. To him a series of prints was like a movie which was an important observation, because it's the control of variation that often weighs down the process with equipment and technique.
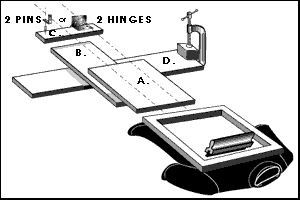
Replacing the newspapers with a board (pallet, A.) enables the deployment of an important trade secret: SPRAY GLUE. Now the shirt can be kept in position to apply more than one color (see the section on 2-pin registration below). Multicolor T-shirt printing is nearly always done with ink in all the screens at once, often wet-on-wet, which is possible because of the aforementioned absorbency of cotton.
With the shirt firmly fastened down it's desirable to locate the screen accurately, which can be done by replacing your friend with a pair of hinges or pins. (Excellent item from the suppliers: JIFFY CLAMPS, hinges with wingnut jaws.) The piece B. creates a space for the tail of the shirt to drop into and enables considerable flexibility in locating pieces A. and C. depending on the size of your screen, plus enabling interchangable pallets. The bottom cross-piece D. should be fastened securely, glued preferably, to B. It allows you to position clamps easily. A big C-clamp on one side serves 2 important functions, or three if it has a sliding bar (which always winds up in the right location in space to hold the screen in it's up position). A block of wood as shown serves to locate one side of the screen perpendicular to the hinges, eliminating racking--a major cause of movement in wood screens.

Here we've come to the point where somebody thought of the carousel printer, which is now the standard device for printing shirts. This machine is basically four or more sets of jiffy clamps mounted on a central pivot, with some sort of registration scheme to bring each screen down in sequence on the pallet. Because each screen can only be supported along one side, the system is vulnerable to the aforementioned racking movement.
I once found myself inside an old-style silkscreen shop where they'd set up twenty or so pallets with 2- pin registration, around a big table. One worker would put shirts on the pallets down the row, followed by others with a succession of screens, with the last person taking shirts off. The modern version of this is an automatic printing machine costing 100K that can be operated by two persons making six dollars an hour, or in Mexico a tenth of that amount.
Fabric printing is very big business indeed: a favorite industry expression is "vertically integrated", which means that an organization has got the entire process, so to speak, under one roof. The plant is almost certainly located somewhere where labor is cheap, which, if the design work is being done elsewhere, compromises the basic principle that the forms things take should evolve from the process of making them. The printed material in fabric stores (which is generally the tailings of the dressmaking industry) looks like the work of low-paid people under a lot of deadline pressure. A lot of these fabrics are printed in China or India, cultures that have produced wonderful fabrics for millenia, but nearly always by craft-based, labor-intensive methods.
Sometimes in old movies a beautiful print shows up--sometimes it's the drapes. The really
interesting fabric prints seem to come from African countries, where women wear
uncut yardage on the street. I carry an image from African fabrics around in my mind:
it's the look of a repeating crescent draped on the human figure.

The 2-pin system is one you design in the aisle of your hardware store. What's needed is a screw with a length of unthreaded shaft that can protude a half inch or so after it's been driven in, the head cut off with a hacksaw and finished by filing a slight bevel around the squared-off end. The second piece is an angle bracket with screw holes slightly smaller than the diameter of the pin so one can be drilled out for a snug fit. Use the hole closest to the angle so there'll be as little wiggle as possible--it's a good device but there still might be enough side-to-side movement to warrent a wood block, or two.
Next I'm going to describe a system that has no inherent movement at all, which to my mind qualifies it as a computer peripheral. The central idea I'm promoting in this site is that screenprinting is a form of computer output if for no other reason than the fact that both present display information the same way--pixels. Since digital images are inherently stable, a printer that can put that image in the same place every time can take what's onscreen into some very interesting places. It's not WYSIWYG--Screenprinting does certain things well and others not at all, but simply the fact that you can screen onto nearly any flat surface is a gigantic advantage over every other kind of computer output
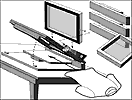

This apparatus takes a little more to build but will accomodate a lot of techniques including 4-color process. I use it to print on paper, fabrics, even objects like electronic housings. I've deliberately not included dimensions other than nominal lumber sizes in order to encourage customization, using scrap material etc.
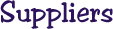
Colors:
- MATSUI International, El Segundo, CA (310)767-7812
- McLogan Supply, Los Angeles. (213)749-2262 Squeegees, emulsion
etc.
- Lambert Co., Boston. (617)628-8150 MANOUKIAN distributor, and etc.
- VERSATEX Siphon Art, POBox710, San Rafael, CA94915
T-Shirt Suppliers:
- T-SHIRT CITY Cincinnati, Ohio/Los Angeles, CA (800)289-5400
- SAN MAR Seattle, WA (800) 426-6399
- VIRGINIA T's (800)289-8099
The Trade:
- SCREEN PRINTING magazine (513)421-2050
- The Imprinted Sportswear Shows (800)527-0207
|